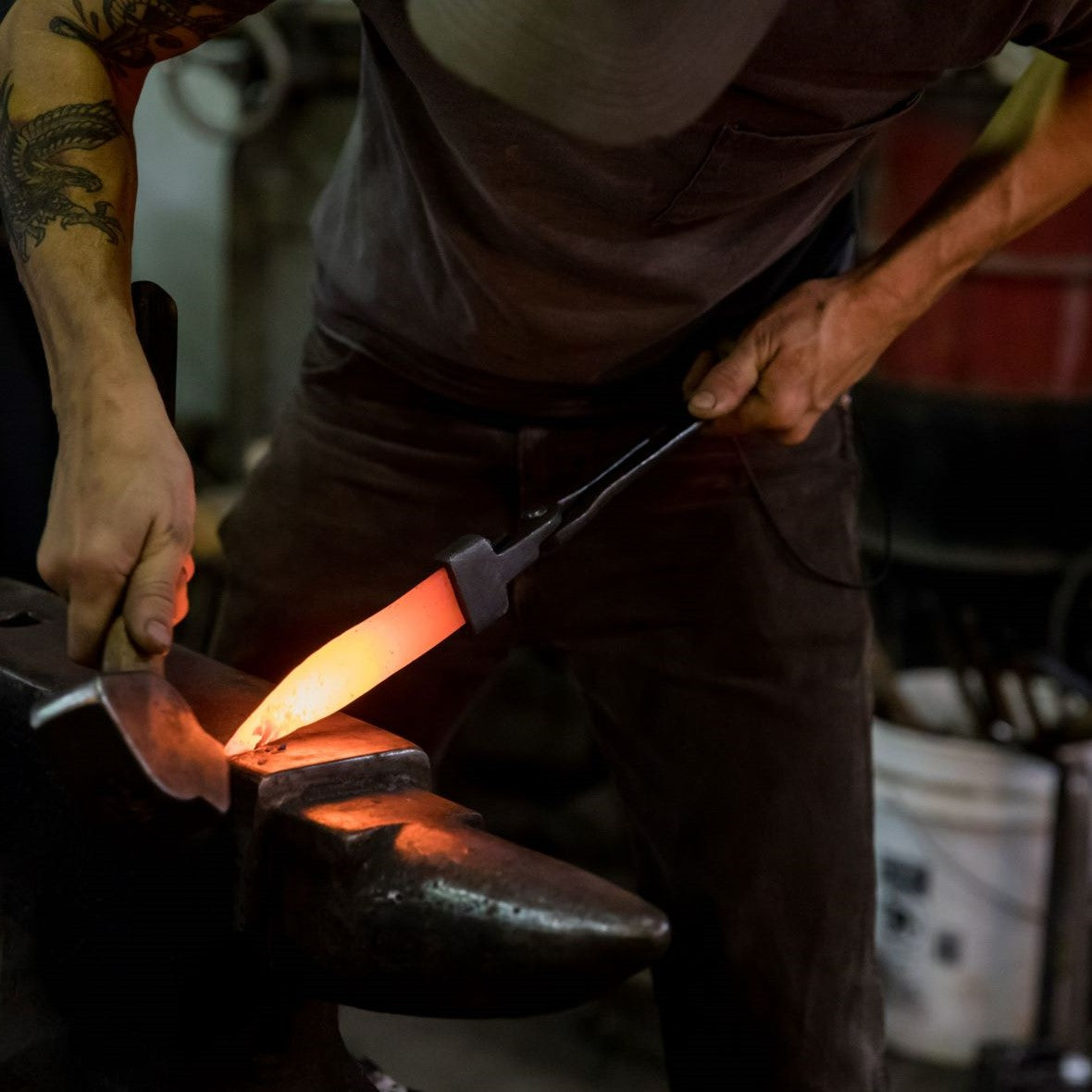
The first tool of man was a knife, well kind of. The Oldowan which takes its name from the discovery site in Tanzania is attributed to early, proto-humans. It is a cobble which is chipped in multiple angles on one side, leaving a hand held chopper in the shape of a rough teardrop. These were used to break bones at kill sites before humans were hunting. They would go in after the animal had finished with the carcasses of the large prey animals such as ancient rhinos and elephants and break open the marrow bones and skull. I have held one of these stones in my hand and at first I must admit that I was skeptical.
“How do you know that is what this is?” I asked my friend Neil.
“Context” he answered. Neil Norman is Associate Professor of Anthropology at the College of William and Mary in Williamsburg Virginia. His main area of archaeological study is west Africa but has also worked in Ethiopia and Tanzania.
“We find these tools at sites that are complete with the chips that came from the tools along with the broken bones. It’s the context that defines these items.”
“When you explain it like that, it makes total sense.” I said
Immediately my sense of what this regular looking rock means shifts. I feel connected to the past in a profound way and start to understand why he carries the thing around in a protective Pelican case. I now know its story and its value. Neil is passionate about his studies in Africa. He has studied the slave trade, toolmaking and other technologies in precolonial Africa and even the origins of Vodon - the progenitor of the Voodoo religion. We met when he took my basic knifemaking class because he wanted to understand more about the process that he studies. We have since met many times and he has shown me some incredible african knives and weapons.
It seems that craftsmanship in Africa has suffered the same fate as it has in the entire developed world, Benin and Nigeria were once home to world’s most advanced cast bronze art. The destabilization of the region following the period of european contact beginning in the early 15th century led to a complete cultural amnesia of the artisanship that these cultures had accomplished. The modern examples of blacksmithing he has brought by the shop are crude tools made with inferior materials. In the current context they do the job but are nothing compared to the works of their ancestors. We too have this same amnesia. At one time, every small hamlet across europe and america had a blacksmith shop which could produce just about anything made of iron or steel that was needed on the farms and shops. Now every small town may have a hobby blacksmith, but most are avocational smiths who are mostly concerned with keeping the traditional skills alive. The masters are fewer and farther between and less appreciated than ever.
Another area that Neil has pursued and helped educate me in has been flint knapping. We talk often of stone points because I love to hunt for them with my sons. The fields and streams of North America are full of stone points and tools left there by the indigenous peoples of this land. Here, context again gives us information about how these tools were made and used. Because of the brittle nature of stone - whether chert, quartzite, flint or obsidian - stone tools are inherently disposable. Knives were designed short and sturdy, sometimes fire treated to make stone more brittle and easier to chip. Tools from the Clovis culture were long thought to be the first stone tools at about 12,000 years old but recent discoveries in 2018 at the Buttermilk Creek site in Texas have confirmed dates of 15,500 years ago and include stone spear points.
Stone tools worldwide show the proliferation of our ancestors' use of the technology. In South Africa, primitive stone blades have been found at sites ranging as far back as 164,000 years ago and predynastic Egypt boasted incredibly worked stone knives 6000 years ago. Other stand-outs are the dagger period knives from Scandinavia of about 3700 years ago and the rich stone tool tradition of pre conquest Central and South America.
Precisely when the basic stone tool which was used for scraping and bashing evolved into what we now think of as a knife is not known. What we do know is that the knife itself is old enough that it doesn't matter. We have been using knives long before the historical period - that is, the dawn of written language. So has anyone ever designed an original knife? The answer is yes and no. To some degree any design has some tiny aspect of originality, some new spark of the creators intent. But to a much greater degree, there is nothing new under the sun. The arc of a knife blade was originally determined by the limit of the material and the practical utility of the shape, featuring both cutting edge and penetrating point.
Metal entered as a material option for knives as early as 6500 BC in the middle east in the form of copper which soon gave way to it's tougher alloy, bronze. These did not immediately outmode stone knives and both were in production simultaneously for thousands of years. While copper knives had to be thick and short to make up for the relative softness and flexibility of the metal, the addition of tin to the copper made for a much stronger blade. Weapons and tools were able to be made longer and thinner with bronze. The early bronze period is dated around
3200 BC. Just as stone tools were still made alongside copper and bronze, so too did bronze persist after the advent of iron around 1800 BC in Anatolia (modern day Turkey). Because of technological difficulties in working with iron, it did not gain widespread use until the roman era.
Steel as we would identify it today was first produced around 500 BC in Anatolia and 200 BC in China. Wootz, Damascus, and Tamahagane are names for early bloom steel which achieved properties of later crucible steel technology. The process of creating iron and then converting to steel or case hardening continued all the way until 1855 when the Bessemer process allowed for large quantities of steel to be produced much more quickly and cheaply. This is also when mild steel began to replace wrought iron as the substance of our metallic built world. Today the Basic Oxygen Steelmaking (BOS) process and electric arc furnaces make steel more efficiently and better than ever.
Powder steel is the newest generation of high alloy steel and is achieved by creating a power out of the steel alloy then forge welding into ingots, thereby producing extremely consistent results which are unachievable with high alloy steels using previous processes. Looking forward, steel alloys will continue to be improved in small increments to be more consistent, harder and more durable. The next wave of technologies in steel production will be in the field of emissions reductions, with many countries committing to reduce carbon footprints across all industries. Using hydrogen as fuel in the furnaces that have traditionally used coal or natural gas is one way to drastically reduce CO2 emissions.
Steel is also still produced by highly skilled artisans in small shops and hammer-ins. The crucible process of producing Wootz type steel is gaining more practitioners, going from an almost extinct craft to one that is attracting more makers every year. Laminating steel to produce what is now called Damascus Steel in knife making shops across the world could almost be called common among a newer generation of makers. Modern Damascus steel differs from ancient Damascus steel in that the ancient production was a secretive cutting edge process to produce the world's best steel and weapons. It was comparable to today’s most advanced military technology. Modern Damascus steel on the other hand is an artistic interpretation of ancient technology. We now use two perfectly good steel alloys to laminate together in the forge welding process to create patterns. This is as opposed to the forging of iron alloys together in order to create a higher quality steel in the ancient process, which left a visible pattern in the surface of the steel.
People often ask me if Damascus steel knives are better than mono steel knives. I usually tell them that it depends on what they mean by better. A damascus steel blade is certainly more visually interesting, takes more skill to produce and is more unique. The durability and edge holding of modern Damascus steel is equal to the steel quality put into the process. Heat treatment and blade design are more important factors. If only the best blade smiths could produce or use damascus steel then the quality would be easier to discern but that is far from the truth. Anyone can buy a piece of Damascus steel or a premade blade blank and make a knife out of it. As has always been, reputation of the maker is the only good way to determine the quality that can be expected from a knife.